Tungsten Carbide Deep Draw Dies
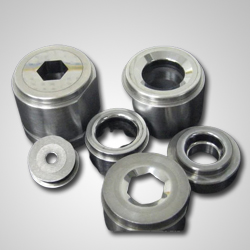
We Mikron Engineers are involved in offering utmost quality of Tungsten Carbide Deep
Draw Dies.
It is crucial to take the bed size and tooling settings into account when selecting
a deep draw die. For instance, the bed of a progressive die press needs to be big
enough to fit the largest footprint of the toolset. The bed must also account for
the orientation of the pieces within the press bed and any space required to shift
the dies. A preliminary estimation of the bed size may be made using the part's
blank size and the amount of material left over for the flanges.
A deep-draw die design provides a number of benefits. The procedure may be carried
out more precisely, resulting in pieces with excellent forming accuracy. To reduce
faults at the corners of the die entry, the geometry and forming characteristics of
the die can be improved. Designing a deep draw die requires taking into account a
number of elements. These considerations include some of the following: The pros and
cons of a deep draw die design will be covered in this article. These suggestions
will help you make the most of your deep-draw die design.
We are Leading Manufacturers, Suppliers, Provider, Exporters, In Mumbai, In Navi
Mumbai, In Thane, In India.
Tungsten carbide wire drawing dies and mould pellets are produced entirely from new WC and
Co. material. It has a strong bending point and good wear resistance.
For large-size wire drawing applications, including applications for drawing wire, tubes,
and rod, tungsten carbide wire drawing dies are a suitable, affordable option. For example,
S11, WTA, S13, etc. Use: for drawing steel wire, aluminium wire, and copper wire